研修の狙い
機械の強度設計に必要な基礎情報、特に設計品質に関わるモデリングの設計指針、いつも悩む材料、許容応力や安全率をどのように設定するか、それらに対する注意点を具体的に 詳しく説明します。これらの情報を有効活用して設計品質を向上させ、製品の品質不具合や事故を防止して頂き、さらに皆様の設計能力を高めて頂きたいと考えております。
研修の目次
1. 機械はなぜ、どのように壊れるのか(破壊事故の原因)
2. 本講座で得られる強度設計の知識
3. 強度設計のプロセス
4. 要求仕様・使用環境条件の明確化
4.1 なぜ製品の破壊が発生するのか
4.2 要求仕様・使用環境条件明確化の注意点
5. 部品設計の設計指針
5.1 応力集中を小さくする形状
① 応力集中率 ② 応力集中の緩和法
5.2 設計対象の工法を考慮した設計
① プレス打抜き部品
(プレス打抜き工法/プレス打抜き部品設計の問題点/
プレス打抜き部品設計の指針)
②プレス曲げ部品
(プレス曲げ工法/プレス曲げ部品設計の問題点/
プレス曲げ部品設計の指針)
③ ダイカスト品・鋳造品
(ダイカスト品・鋳造品の工程/ダイカスト品・鋳造品設計の問題点/
ダイカスト品・鋳造品部品設計の指針)
④ プラスチック部品
(プラスチック部品の製造工程/プラスチック部品設計の問題点/
プラスチック部品設計の指針)
6. 強度設計のための材料選定
6.1 材料選定のポイント
6.2 機能展開からの材料選定
6.3 材料選定基準
6.4 材料選定に対する注意点
6.5 海外鉄鋼メーカの材料き裂の事例
6.6 鉄鋼材料
① 鉄鋼材料の分類
② 鉄鋼材料の製造工程
③ 普通鋼
④ 合金鋼
⑤ 金属の危険な破壊
6.7 アルミニウム合金
① アルミニウム合金の製造工程
② アルミニウム合金の種類
③ アルミニウム合金の危険な破壊
6.8 金属の熱処理
① 金属の熱処理の分類
② 金属の一般熱処理
③ 金属の表面硬化熱処理
6.9 表面処理
① 表面処理の種類
② 表面処理の比較
6.10 焼結材
① 焼結材の位置づけ
② 焼結材の特徴
③ 焼結材の製造工程
④ 焼結材の種類
⑤ 焼結材選定時の注意
6.11 プラスチック
① プラスチックの特徴
② プラスチックの特性を左右する要因
③ プラスチックの種類
④ プラスチック選定時の注意
⑤ 外装モールドコイルの樹脂流れ不良の事例
6.12 ゴム
① ゴムの特徴
② ゴムの構成
③ ゴムの種類
④ ゴム選定時の注意
⑥ Oリングき裂の事例
7 強度評価
7.1 なぜ製品の破壊が発生するのか
7.2 強度評価の手順
7.3 製品の構造体に発生する負荷応力を求める時の注意
7.4 材料の基準強さ
7.5 安全率
7.6 疲労限度線図
7.7 ターボチャージャのタービン翼設計
① ターボチャージャとは
② タービン構造
③ タービン翼設計の注意点
④ タービン翼に加わる力
⑤ タービン翼の応力解析
⑥ タービン翼の共振
⑦ 疲労限度線図
⑧ タービン翼のクリープ特性
7ー8. 高圧燃料供給システムの設計
① 高圧燃料供給システムとは
② 高圧燃料供給システムの低騒音化設計
③ 不具合現象
④ 不具合原因
⑤ 不具合対策
7ー9. 銅ロー付け部の疲労強度設計
① 設計や信頼性評価で考慮すべき点
② 疲労強度評価
8. 過去のトラブル事例集の活用
① 過去のトラブル事例集とは
② 過去のトラブル事例集で重要なこと
③ 過去のトラブル事例集の活用方法
9. デザインレビューの活用
① デザインレビューの目的
② デザインレビューの実施時期
③ デザインレビューへの参加者
④ デザインレビューに使うもの
⑤ デザインレビューの意義
⑥ デザインレビューで議論すべき不具合防止の教訓
10. おわりに
研修方式
ウェブ方式(TeamsあるいはZoomを使用)
あるいは 対面方式
研修への参加人数
1人から30人位 相談します。
研修時間
6時間
実施時間は相談の上、決めます。
研修費用
6時間研修:37,000円/人
(源泉徴収税、消費税を含む)
グループ受講の場合は相談して決めます。
製品事故の原因
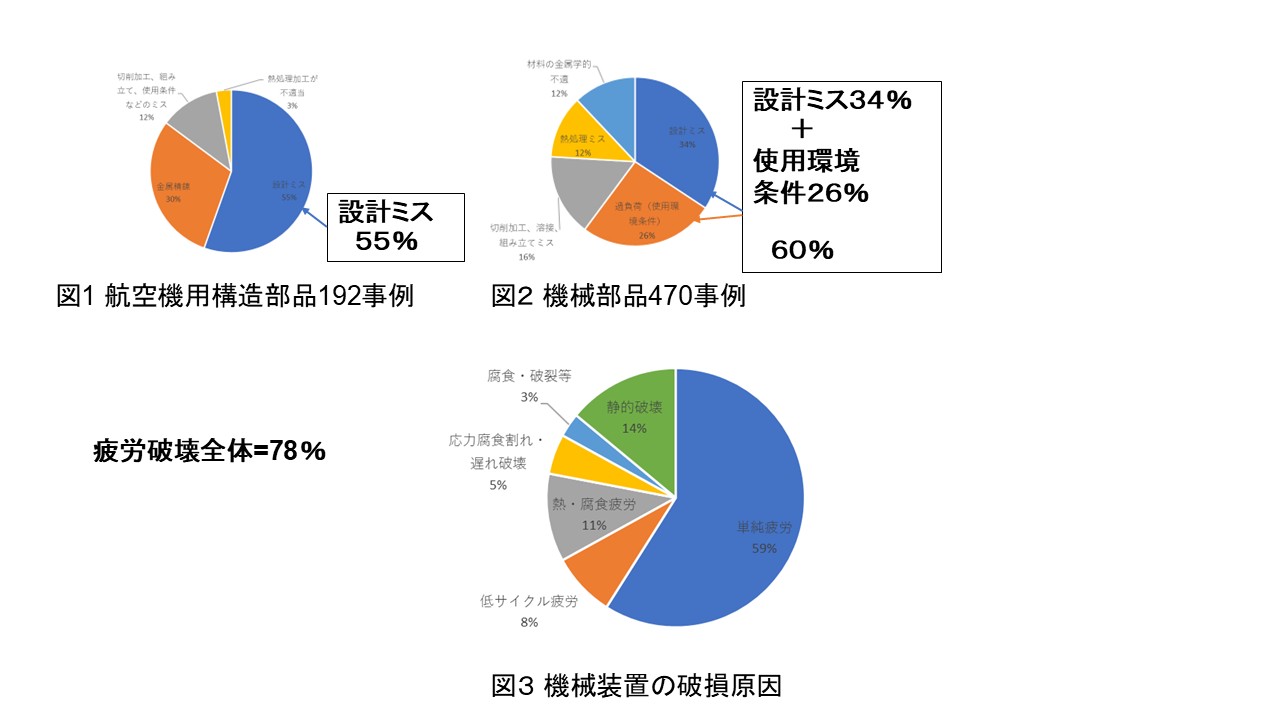
破壊しているのでしょうか?
1.まず製品の破壊の原因がどこにあるかを
見ます。
航空機用構造部品192事例を見ると
設計起因が55%、その他は
製造起因です。(図1)
機械部品470事例では設計ミスが34%、
使用環境条件の誤りが26%、
使用環境条件は設計が決めますので、
設計起因は60%となります。
その他は製造起因です。(図2)
2.次に、破壊の原因がどのような
破壊形態かを見ます。
機械装置の破損の原因を見て見ると、
単純疲労が59%、低サイクル疲労が8%、
熱・腐食疲労が11%で
疲労破壊が78%を占めています。(図3)
3.設計活動を改善し、疲労破壊についての
知識を学び、疲労破壊を起こさない
設計をやれば、製品の破壊や事故を
低減できるのではないでしょうか?
強度設計のプロセス
主に下記項目から構成されます。
(1)要求仕様・使用環境条件の明確化
設計対象に対する要求仕様と設計対象が
使用される環境条件を調査
(2)設計対象のモデリングと図面
(3Dあるいは2D)
設計対象が要求される機能を発揮
できるように設計対象をモデリング
設計指針を活用
(3)材料選定
機能や要求仕様を満足し、
使用環境条件に耐える材料を選定。
(4)強度解析
有限要素解析などで応力やひずみの
分布を算出。
(5)強度解析結果の評価
安全率と基準応力許容応力
設計対象に加わる応力<許容応力 を
確認。
設計対象に加わる応力>許容応力 の場合
モデルか材料を改善。
(6)信頼性評価
試作品を使い要求仕様を満足することを
実験で検証。
研修の目的
1)強度設計プロセスと、そのプロセスの中で
設計をするために重要なポイントを
明確にして破壊事故を減らすことに貢献
する。
(2)設計で設計品質に関わるモデリングの
設計指針、いつも悩む材料選定や
許容応力や安全率をどのように設定
するかを明確にする。
(3)破壊事故を防ぐ設計ができるような
仕掛けを提供する。
要求仕様・使用環境条件明確化の注意点
する時顧客要求仕様だけに限らず
設計対象の環境条件を調査することが
重要です。自分の製品がどのような
条件や環境で使われるかを自分で
考えるべきと考えています。
2.顧客要求仕様や使用環境条件を整理する
方法として設計FMEA不具合ポテンシャル
に対しそれらを整理するやり方が
あります。設計FMEAに設計検証の欄と
実験検証の欄を設けて、顧客要求仕様や
使用環境条件を設計検証の欄に記載、
その確認結果を実験検証の欄に記載
するのが良いと考えています。
部品の強度設計指針

図面を作成する時、応力集中を
なくす設計が必要です。
角部にはRをつけて応力集中を
低減する必要があります。
この研修では、いろいろな
荷重に対する応力集中率を
説明して、応力集中を減らす
アイデアも提示しています。
2.また、信頼性を確保するため、
設計対象部品の製造工程に
おいて気をつけるべき事が
あります。それらは経験に
基づき蓄積されたものもあります。
3.例えば、上記の図には
プレス打抜き部品の設計に起因する
問題点の1例を示しています。
この問題に対して、ダイの破損を
防止するために最小寸法Wに対し
設計指針があります。
4.この研修では、このような設計
指針を下記部品に対して説明
しています。
(1)プレス打抜き部品
(2)プレス曲げ部品
(3)ダイカスト品・鋳造品
(4)プラスチック部品
材料選定
(1)機能や要求仕様を満足し、
使用環境条件に耐える、
(2)品質、生産性、供給安定性、
経済性の観点から最適で
あることです。
2.この研修では、機能展開からの
材料選定の例を示し、さらに
材料選定基準、材料選定に対する
注意点を詳しく説明しています。
そして、材料にき裂は入った時の
原因追及と対策に事例を説明して
います。
3.この研修では、鉄鋼材料、
アルミニウム合金、金属の
熱処理、表面処理、焼結材、
プラチック、ゴムについて
種類、特徴、製造工程、選定の
注意点などを詳しく説明して
います。鉄鋼、アルミニウム
合金については、危険な破壊
を示し、ゴムのOリングの
き裂の事例を説明しています。
強度評価
(1)製品の構造体に発生する
負荷応力σL を求める。
(2)材料の基準強さを調べる。
(3)安全率と基準強さから
製品の構造体の許容応力 を
求める。
(4)負荷応力が許容応力より
小さいことを確認する。
2.この研修では、材料にかかる
荷重の種類から材料の基準強さを
どのように設定するか、そして、
安全率を具体的にどのように設定
するか、安全率を低く抑えるには
どのようにするか、等を具体的に
説明しています。
3.ターボチャージャのタービン翼
設計の事例では、疲労限度線図
を使い疲労強度設計を、さらに
クリープ強度評価を詳しく説明
しています。
失敗を起こさない仕組み
過去のトラブル事例集の活用と
デザインレビューの活用は非常に
重要だと考えております。
詳細は研修で説明します。
2.費用は37,000円/人
(源泉徴収税、消費税を含む)です。